Jacketed Glass Reactor Vessel For Stirred Reaction
1 Common types of reactors
According to the manufacturing structure of the reactor, it can be divided into three categories: glass phase reactor, glass-lined reactor and stainless steel lab reactor . Each structure has its scope of application and advantages and disadvantages. According to the material and use of the reactor, there are the following types:
1.1 Jacketed glass stirred reactor
The static seal structure is adopted, and the magnetic coupling is used between the stirrer and the motor drive. Due to its non-contact transmission torque, the static seal replaces the dynamic seal, which can completely solve the leakage problem that cannot be solved by the previous mechanical seal and packing seal. Each stirring part works in an absolutely sealed state.The most ideal leak-free reaction equipment for vulcanization, fluorination, hydrogenation, oxidation and other reactions in polymer material polymerization, food and other processes.
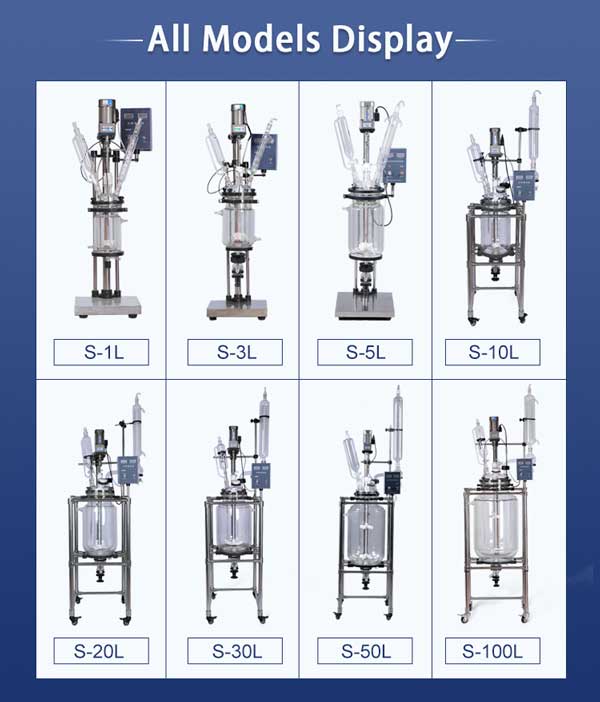
1.2 Stainless steel reactor
The materials are generally carbon-manganese steel, stainless steel, zirconium, nickel-based (Hastelloy, Monel) alloys and other composite materials: according to the manufacturing structure of the glass reactor assembly, it can be divided into open flat-cover type reactor, open butt welding flange type There are three types of reactors and closed reactors. Stainless steel, the stirring form of the reaction kettle is generally anchor type, paddle type, turbine type, propeller type or frame type, etc. When the stirring device is relatively large in height and diameter, multi-layer stirring blades can be used, and can also be selected according to user requirements. . The different sealing types of stainless steel reaction kettles can be divided into: packing seals, mechanical seals and magnetic seals.The cooling methods are jacket cooling and inner coil cooling in the kettle. Stainless steel reactors are widely used in petroleum, chemical, rubber, pesticides, dyes, medicine, food, and pressure vessels used to complete processes such as vulcanization, hydrogenation, alkylation, polymerization, and condensation, such as reactors, reactors, decomposition pots, Polymerization kettle, etc.
1.3 Glass-lined reactor
The glass-lined reactor is a composite product made by lining the inner surface of a steel container with glass containing high silica, which is firmly adhered to the metal surface after being burned at a high temperature. Therefore, the glass-lined reactor has the dual advantages of glass stability and metal strength, and is an excellent corrosion-resistant equipment. Glass-lined reactor technical specifications: working pressure: 0.2---0.8Mpa; acid resistance: good corrosion resistance to various organic acids, inorganic acids and organic solvents: alkali resistance: glass-lined to alkaline solutions Corrosion resistance is poorer than acid solution. Glass-lined has good insulation. When the glass-lined is inspected with 20KV high-frequency electric spark within the specified thickness, the high-frequency electric spark cannot break down the ceramic layer. Impact resistance: The smaller the internal stress of the glass layer, the more elastic it is. Well, the greater the hardness, the higher the flexural and compressive strength, and the better the impact resistance.
This article will specifically introduce the jacketed glass reactor vessel for stirred reaction.
2 jacketed glass reactor vessel for stirred reaction
Stirring reactor is one of the typical reaction equipment commonly used in chemical, pharmaceutical and food industries. It is a device that mixes two (or more) liquids and liquids and liquids and solid or gas materials with a certain volume under a certain pressure and temperature with the aid of a stirrer to promote their chemical reaction, usually accompanied by Thermal effect, the required heat input or the generated heat removed by the heat exchange device. The stirring reaction kettle can be divided into vertical, horizontal, inclined and bottom stirring according to the installation type of the stirring device; according to the stirring form, it can be divided into paddle type, frame type, anchor type, propeller type, turbine type, etc. According to the requirements of the design task book, the stirring reactor designed this time is a paddle stirring reactor. The structure of the paddle stirring reactor is relatively simple. Its stirring blade is generally made of flat steel. When the material in the kettle is significantly corrosive to carbon steel, it can be made of alloy steel or non-ferrous metal, or it can be made of steel. Outsourcing banana or epoxy resin, phenolic glass cloth and other methods. The blade installation form is divided into two types: straight blade and folded blade. A straight leaf is the relationship between the leaf surface and the direction of rotation.
are perpendicular to each other; the hinges are inclined at an angle to the direction of rotation. The straight blade mainly makes the material flow in the tangential direction, and after adding the stirring baffle, it can produce a certain axial stirring effect. Folded leaves have slightly more axial diversion than straight leaves. The operating speed of the paddle agitator is relatively slow, generally 10-100 r/min, and the peripheral speed is suitable in the range of 1.5-3 m/s. It is widely used to promote the mixing and dissolution of heat transfer soluble solids and is very effective when slow stirring is required, such as stirring of mixed liquids and liquids with solid particles.
2.1Advantages of jacketed glass reactor vessel for stirred reaction
Features With the gradual increase of the volume of the large-capacity glass-lined (jacketed kettle wall) reaction vessel, the ratio of the heat exchange area of the jacketed kettle wall to the unit volume in the vessel is decreasing. As the volume increases, the heat exchange area per unit volume gradually decreases, and the heat exchange area with a volume of 40,000L is only 42% of the heat exchange area with a volume of 3,000L. The reduction of the heat exchange area of the jacket of the reaction vessel will greatly affect the cooling and heating speed of the reaction process, which in turn affects the reaction speed, reaction time and yield. The S-type heat exchange area is reduced even more.
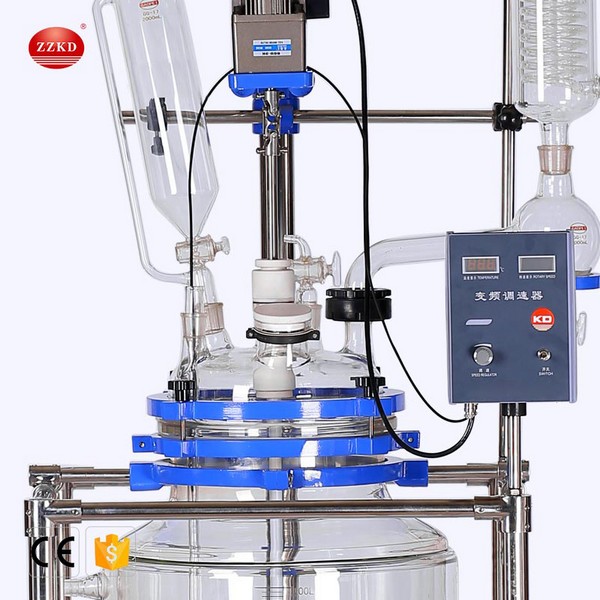
2.2 The method of improving the reaction speed of glass stirring reaction vessel
The method to improve the reaction speed of a large-capacity glass-lined agitated reaction vessel is to increase the heat transfer rate of the vessel. After the container is enlarged,
The heat transfer area per unit volume is reduced, so increasing the overall heat transfer coefficient is the best way to improve the heat transfer effect.
2.3 Structure description of glass stirring reaction vessel:
In order to improve the heat transfer effect of the reaction vessel and reduce the thickness of the cylinder, the most effective method is to reduce the calculation length of the external pressure of the circular simple, so
It is necessary to set a certain number of reinforcing rings for the inner cylinder. Due to the requirement of the rationality of the structure of the clamping sleeve body, the gap between the inner tube and the clamping sleeve body cannot be too large, and the structural size of the reinforcing ring is therefore limited. Usually, low-pressure steam is used as the medium in the jacket. Due to the low design external pressure of the inner cylinder, the gap between the inner cylinder and the jacket is sufficient to meet the requirements of the structural size of the reinforcement ring and the flow area of steam and its condensate.
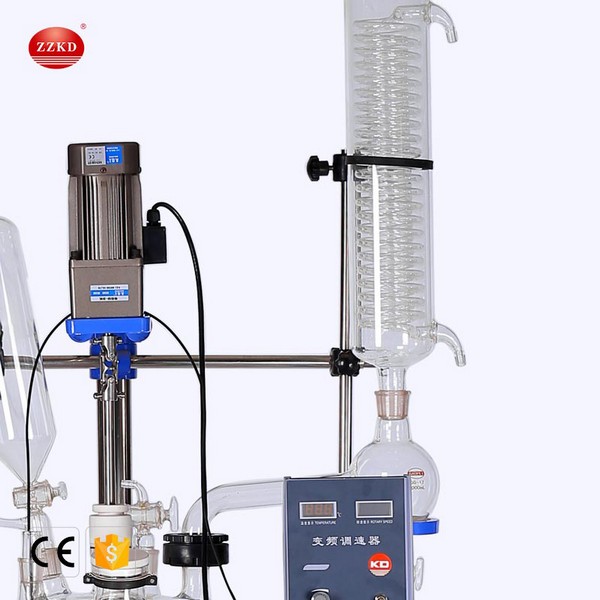
3 Features of jacketed glass reactor vessel for stirred reaction:
●This product is the advanced, ideal and practical of our company at home and abroad. The triple elastic design of the support frame ensures the reaction operation under heavy load, and is compatible with the safety of lifting and changing.
●Using high borosilicate glass material (GG17), with excellent physical and chemical properties.
●It can be used in high temperature range from 200℃ to low temperature -80℃.
●Advanced frequency conversion speed regulation, frequency conversion controller, internal components have vacuum coating protection, corrosion resistance, optional full explosion-proof, safe and reliable.
●The kettle body has two layers, and the heat source and cooling liquid are used in the middle of the interlayer to provide the needs for the reaction. Three-layer kettle body, the first layer is the vacuum interlayer kettle body for thermal insulation, and the second layer provides heat and cold satisfaction for the reflection. The fully transparent reaction bottle can make the reaction process clear at a glance.
●Polytetrafluoroethylene (PTFE) components are sealed and specially designed to maintain the vacuum degree of similar products in the market (about -0.098mpa). The discharge valve can discharge concentrated liquid and trace solid materials.
●The jacket pressure control device is the company's new technology for the protection of the kettle body, which makes the work safe and reliable.
●The kettle cavity and jacket are designed to have no dead angle, anti-corrosion and pollution-free structure.
●The heat transfer medium can be completely removed after the reaction is completed, and there is no effusion.
●This product has a scientific structure, beautiful and practical.